
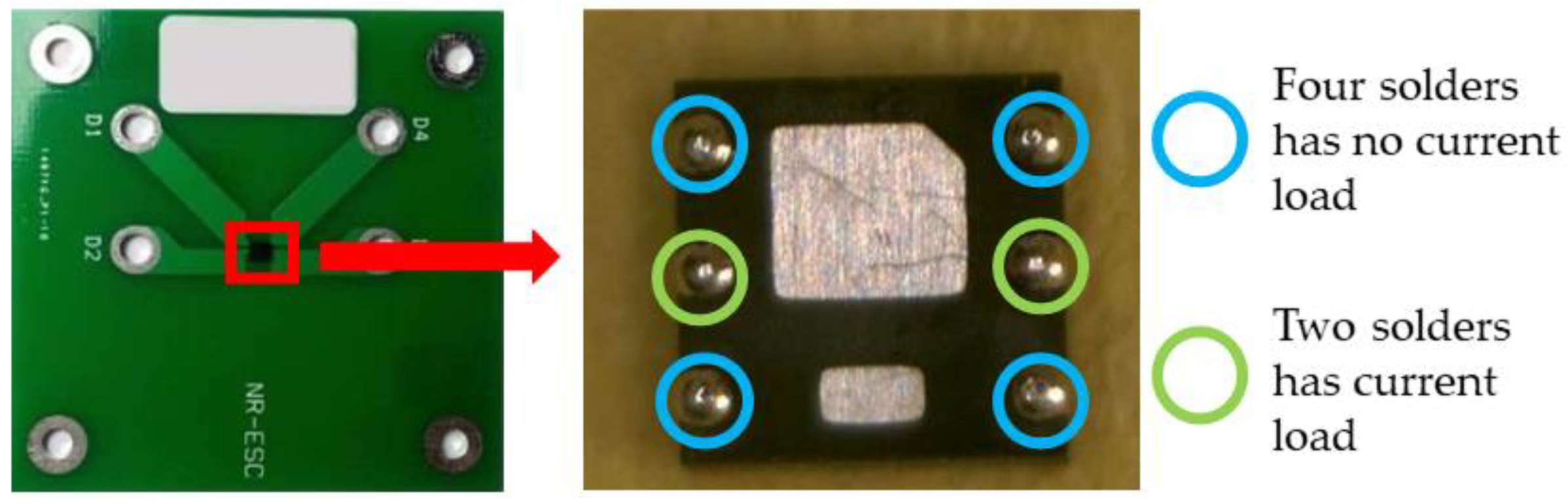
The overarching challenge is to design alloys that are compatible with the unique additive processing conditions while maintaining material properties sufficient for the challenging environments encountered in energy, space, and nuclear applications. The lower creep properties of Nb-modified alloy at T > 800 oC should be primarily associated with higher internal diffusivity in this alloy compared to the conventional one, leading to faster oxidation and microstructure degradation during the high temperature creep.Īdditive manufacturing promises a major transformation of the production of high economic value metallic materials, enabling innovative, geometrically complex designs with minimal material waste. Both alloys have a better creep life in high vacuum which revealed an important role of oxidation on the creep damage mechanisms of these alloys. At 900 ☌ and 1000 ☌, the conventional alloy has shown better properties associated with less creep damages in the bulk and near the surface regions. Both alloys presented similar creep behavior at 800 ☌. Additional creep tests were carried out at 900 ☌/350 MPa under high vacuum conditions to verify effects of oxidation on the creep behavior of the alloys. Conventional and Nb-modified polycrystalline MAR-M246 superalloys were prepared through vacuum induction melting and investment casting from commercial raw-materials. The obtained results confirm the strong potential of the SSCG technique coupled with SPS for the growth of undoped and highly doped YAG single crystals with excellent quality.Considering the lower cost of Nb and its chemical similarity to Ta, this work investigated the effect of complete replacement of Ta by Nb (in at.% basis) in MAR-M246 Ni-based superalloy for the automotive turbocharger applications. EDS elemental mapping and line scans confirmed the compositional uniformity of the grown single crystals, while EBSD images verified their crystallization in the (110) direction. Moreover, high Nd 3+ doping levels had a positive effect on the conversion kinetics, with a growth rate of almost 50 µm/h, which increased the driving force for single-crystal growth through the solute drag effect. The application of external pressure during the SPS process has been found beneficial for reducing the porosity of the grown single crystals. The growth of single crystals was initiated at the surface of (110) YAG single-crystal seeds embedded inside YAG and Nd:YAG powder beds, and this growth continued as the surrounding polycrystalline matrix was converted into a single crystal. In this work, Y 3Al 5O 12 (YAG) and Nd 3+-doped YAG (Nd:YAG) single crystals were grown via the SSCG method using spark plasma sintering (SPS). Recent studies have shown that many challenges encountered in conventional single crystal growth methods, including high production costs, can be overcome by using the solid-state single-crystal growth (SSCG) approach, which has been recognized as a simple and cost-effective alternative for obtaining single crystals.
